Xypex Projects
From subway stations to swimming pools, from bridges to buildings, and in foundations, critical infrastructure, and many other applications around the world, explore our always expanding list of Project Profiles to learn how Xypex Crystalline Technology waterproofs, protects and repairs concrete.
Find Projects
.jpg)
Couvrette Park – Aquatic Facilities and Chalet Construction
The City of Laval is revitalizing Couvrette Park to enhance recreational offerings and strengthen community infrastructure. The redevelopment plan includes the construction of a multifunctional chalet for all four seasons and modern aquatic facilities, creating a contemporary and accessible space for residents.
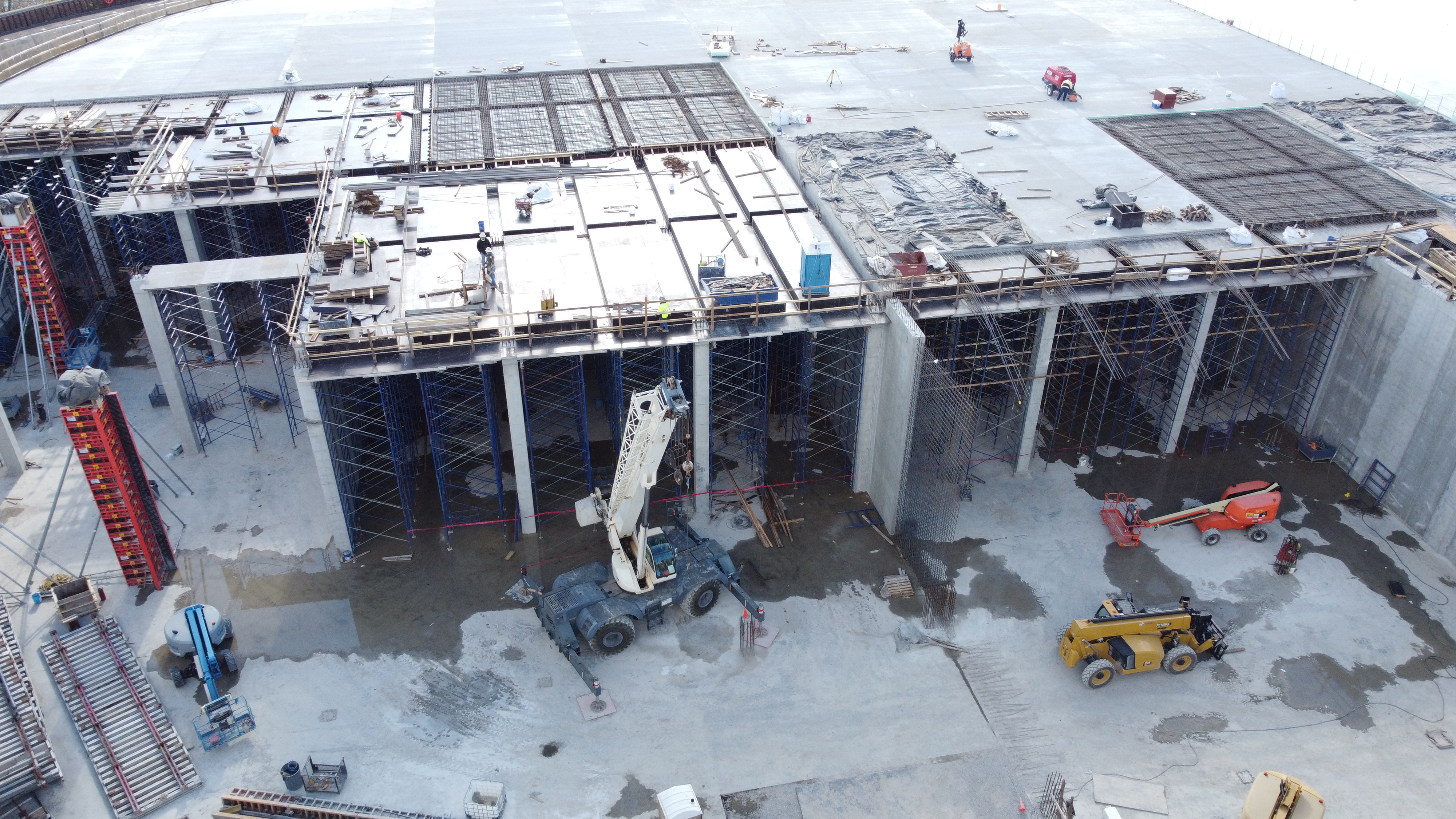
8th Ave Reservoir Improvements
Initially built in 1889, the 8th Avenue Reservoir is the largest and oldest of the city's 37 reservoirs, supplying clean drinking water. Bowen Engineering chose Xypex Admix C-500 NF for its proven, durable, long-lasting waterproofing performance as part of a comprehensive rehabilitation project, including tank-in-a-tank construction, vault improvements, and overall reservoir upgrades.
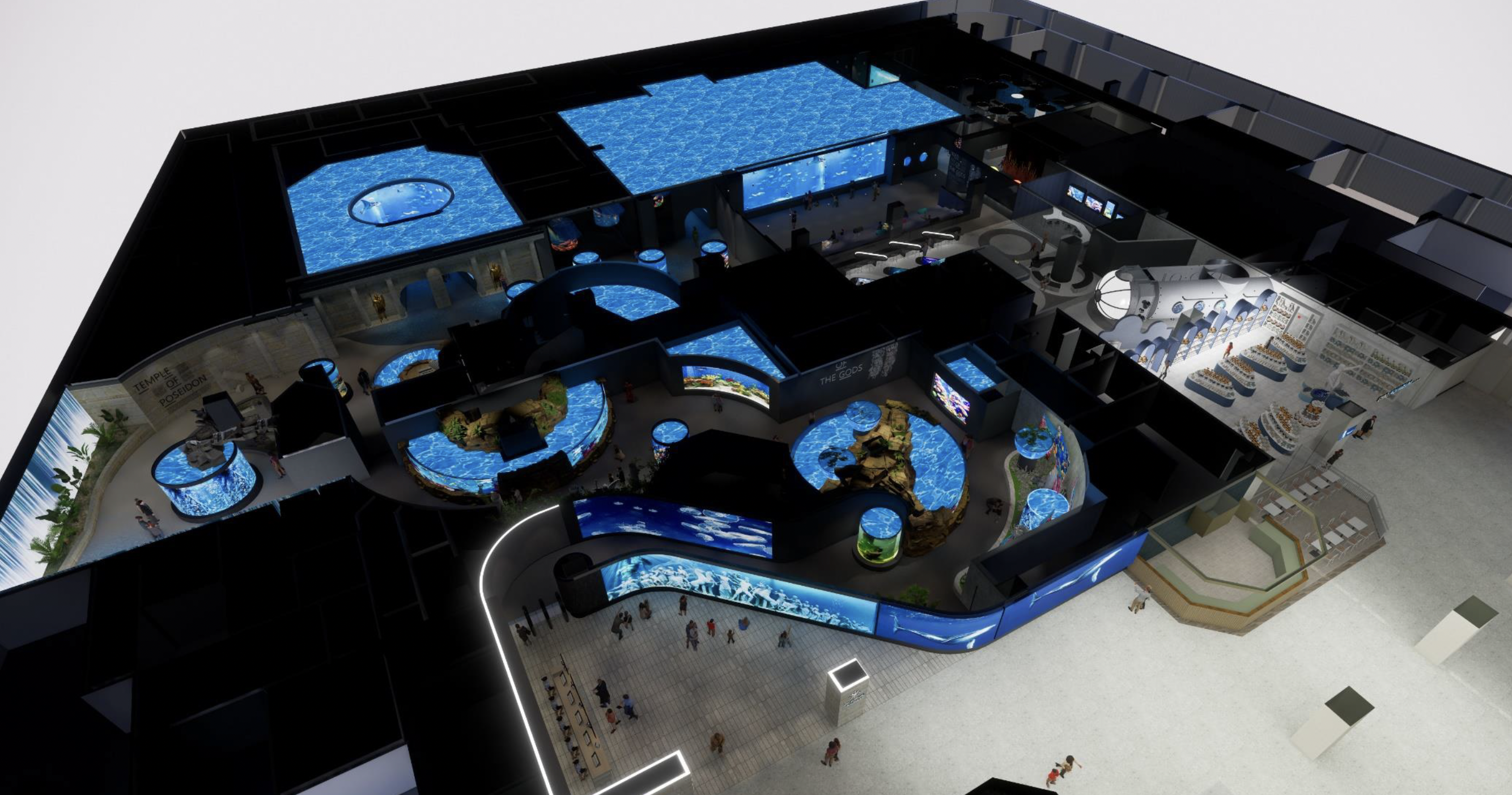
Daejeon Expo Aquarium
The Daejeon Expo Aquarium, located on the first basement floor of the Daejeon Science Complex in Daejeon City, Korea, spans 6,623 square meters and has quickly become a prominent attraction. This new construction features a unique two-floor design, including a 94-meter-long submerged tunnel offering panoramic views of marine life.
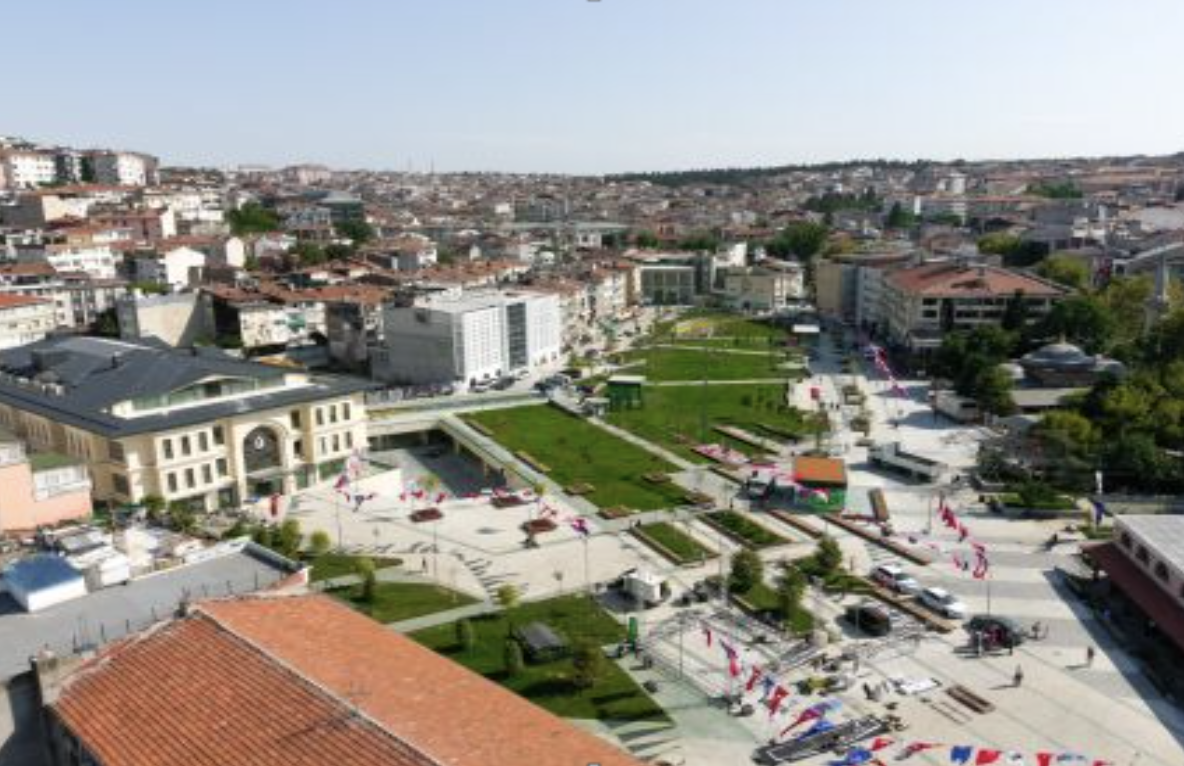
Mimar Sinan 4-Storey Underground Parkade
The Mimar Sinan Underground Parkade, completed in 2023 as an initiative of the Istanbul Metropolitan Municipality, lies beneath the newly developed Mimar Sinan Square in Istanbul’s historic Üsküdar district. Extending over four underground levels and accommodating up to 956 vehicles, this facilitydirectly addresses long-standing parking shortages, eases local traffic congestion, and bolsters urban infrastructure.
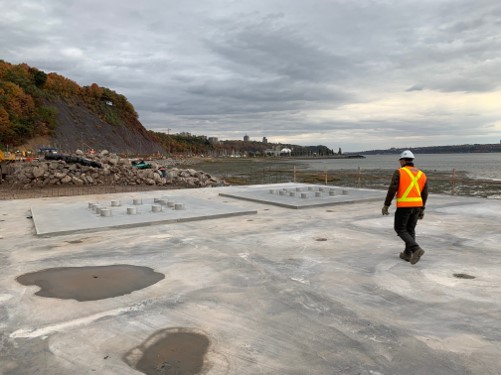
Promenade Samuel-de- Champlain Phase 3
As part of the Phase 3 redevelopment of the Promenade Samuel-De Champlain Phase 3 along the St. Lawrence River, the Beach Station features a public swimming pool designed to reconnect the community with its waterfront heritage. To meet the high-performance expectations, Groupe Deric SIÈGE SOCIAL, the appointed contractor, strategically selected Xypex Concentrate for the construction and integral waterproofing of the swimming pool.